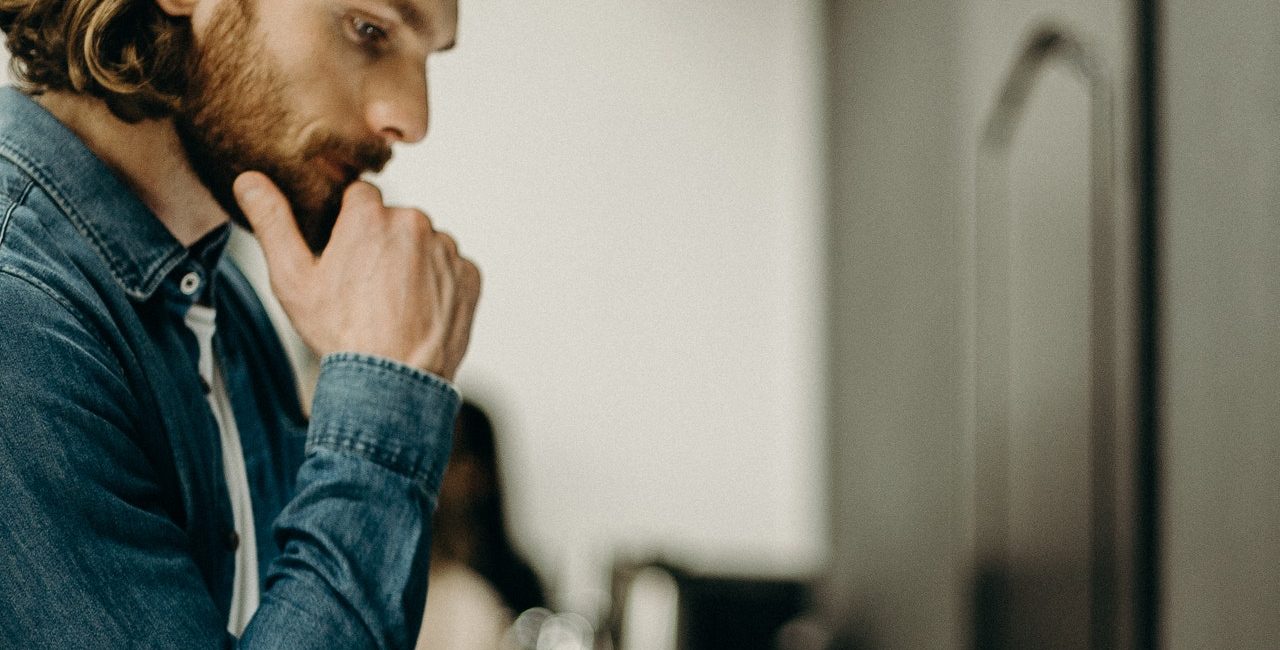
When it comes to creating a printed product – be it packaging, corporate stationery, marketing materials, or informational posters – it is not enough to hit ‘print’ and move on. Print finishing has the potential to bring your printed products to the next level. So, without further ado, let’s take a look at the top 7 print finishing techniques.
Cutting and creasing
Cutting and creasing is exactly how it sounds – printed pages can be created for the ease of folding, or cut to the desired shape. Cutting can either be achieved by hand using a pair of scissors, using a guillotine or, for more intricate designs, by using a die cutter. The technique for each process is very similar, with the only difference being that sharp blades are used for cutting, whereas dull, blunt blades are used for creasing.
Varnishing
You might be most familiar with the effect varnishes have on printed products when considering the likes of fashion catalogues, magazines, and brochures. However, varnishes come in many different finishes, not just gloss. Depending on the type of print you have made, you may also consider matte, silk, UV, textured, or machine sealed varnishes for your print finishing.
Lamination
Lamination is most typically used to prolong the lifespan of a printed product. A thin layer of matte or gloss clear plastic is placed on each side and then sealed using heat. This creates a durable protective finish for the printed page, keeping it safe from any drops and spills.
Embossing
Embossing uses specialist print finishing equipment to raise specific parts of the printed page with a stamp and some pressure. This can be used subtly for texture, to highlight certain aspects of the design, or to create a 3D effect. Overall, it takes printed products to the next level by introducing a tactile element to the design.
Debossing
As you might imagine, debossing is essentially the opposite of embossing. Instead of raising aspects of the design, debossing will indent or depress the page. This technique was derived from the early printing press techniques, and so can also be referred to as a letterpress. That being said, it is not confined to only printing letters – it is commonly used for pressing logos and tactile designs, too.
Foiling
Stamping a metallic foil onto your printed products is a simple way to make prints look more high-end and expensive. The foil is stamped onto the page with heat and pressure, sticking it to the places in the design you want to highlight. These foils come in a wide variety of different colours, including gold, silver, rose gold, every colour imaginable, and even holographic.
Thermographic powder
Thermography refers to using heat to raise the level of a printed product, creating a similar effect to embossing without the need for a custom stamp. Thermographic powder is available in a wide range of colours and finishes, including metallic powder, glitter powder, and fluorescent powder, all of which can be used to highlight the main areas of your printed design.
And there you have it – just a quick ‘print-ro’ into the top 7 print finishing techniques. With this in mind, you will be able to transform your printed materials into eye-catching designs in no time.