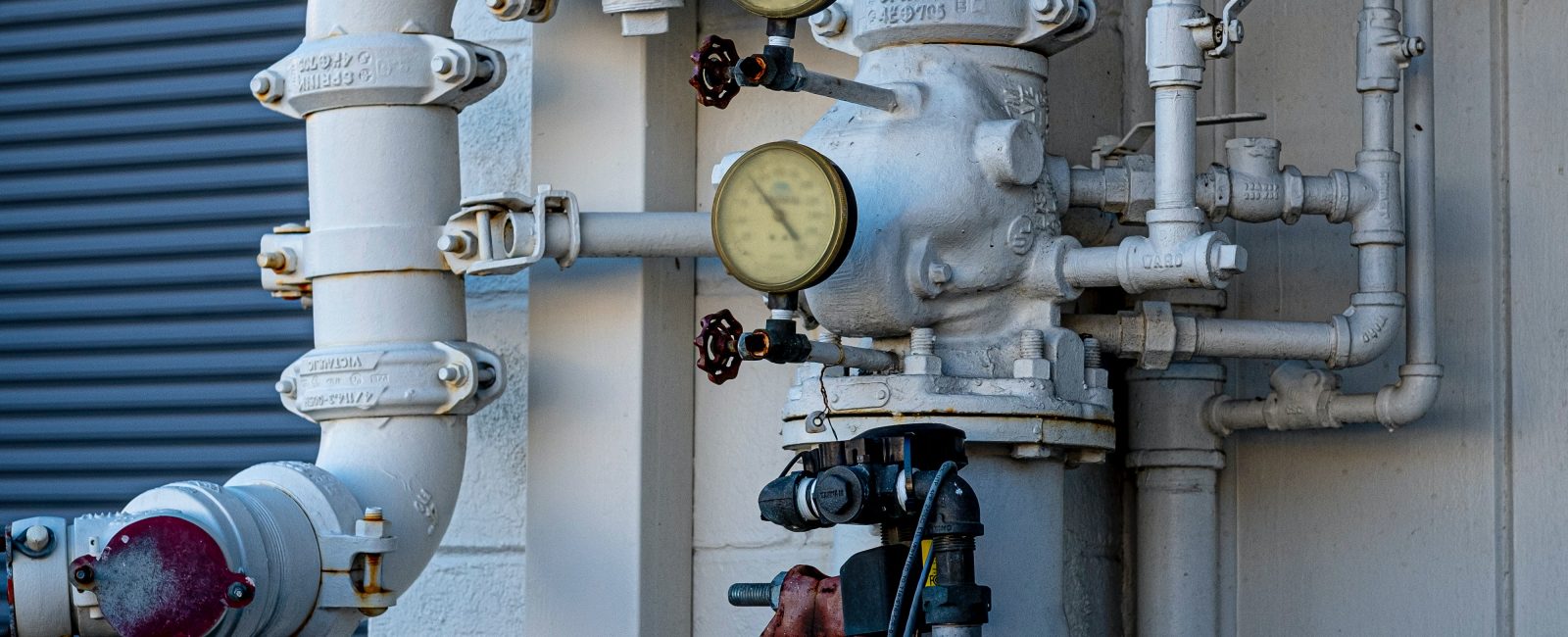
Industrial valves are used in a wide range of applications. They control the flow of liquids, gases, or steam over varying pressures and temperatures. Typical use cases of industrial valves include: diverting flow around a system component for maintenance purposes, preventing the backflow of fluids, and helping isolate piping sections during maintenance.
Depending on your industry, unique system requirements, and personal preferences, you can choose one or a combination of valves that will guarantee safe and optimal operation.
Popular industrial valves are gate valves, check valves, ball valves, butterfly valves, and globe valves. We have discussed these valves, their operation, and their applications in the sections below.
Types of Industrial Valves
The industrial valves we will discuss are operated manually or automatically. Automatic types use either electricity or hydraulics/pneumatics. Pneumatically-operated valves are ideal in most industrial applications since they are versatile and offer rapid opening and closing. They also operate at a wide range of temperatures and pressure ranges and are more durable and reliable.
Ball Valves
Ball valves are a type of valve that uses a metallic ball to control/regulate the flow of liquids or gases through a pipeline. The ball valve consists of a valve stem connected to a lever, the main valve body, a disc-shaped valve seat, and a ball held in position by the seat valve and O-springs. When the handle is rotated quarter-turn, it either opens or closes the valve.
Ball valves are commonly used in liquid-handling applications, including water purification systems and industrial processes. Due to the valve’s unobstructed flow, durability, and low-pressure drop, it’s commonly used as a shut-off valve.
Gate Valves
Gate valves are one of the simplest types of valves, and they’re commonly used in almost every industry. Gate valves work by using a gate that moves up/down on the stem depending on the hand wheel’s direction. When the gate is lifted, the inlet opens and connects to the outlet, allowing for unobstructed fluid flow, and vice versa is true.
Types of gate valves include wedge, knife, parallel-slide, and slab gate valves. These valves have several advantages over other types, including unobstructed fluid flow, relatively low cost, and ease of use. These valves are, however, not suitable for high-pressure applications and are not ideal for regulating fluid. Gate valves can be used with slurries and viscous media.
Check Valves
These are one-way valves that prevent the backflow of fluids in a system. They are cheap and effective, making them popular in most industries. Check valves are either normally closed or normally open; the right one for you will depend on your unique applications.
Typically, the valve requires some pressure differential (called cracking pressure) between the inlet and outlet. When there’s back pressure or the upstream pressure goes below the cracking pressure, the check valve closes. Types of check valves include spring-loaded in-line, Ball, Diaphragm, Lift, Swing, and spring-loaded Y-check valves. Each of these valves finds ideal application in different settings. It’s therefore important to consult before picking one.
Butterfly Valves
These are quarter-rune valves used for on-off operations and for modulating fluid flow. Butterfly valves are cheap, lightweight, and with a smaller footprint. When the valve’s handle is rotated, a stem rotates the disc from a closed to an open position and vice versa. The various butterfly valves are classified based on the disc closure design, connection design, and action method.
Butterfly valve advantages include good sealing, hygienic design, and ease of cleaning. These valves, however, are not ideal for high-pressure applications. Typical industries you’ll find butterfly valves include food processing or any system with clean-in-place technology.
Globe Valves
Globe valves are commonly used for regulating or mixing fluid media thanks to their good flow and regulating properties. When the knob is turned, it moves the stem and the plunger up or down, opening/closing the valve.
You’ll also find safety and pressure relief valves in the market. The two serve almost the same purpose (helping avoid high-pressure situations, which could lead to damages and injuries), but they operate differently.
Choosing the Right Industrial Valve for Your Application
Valves are a critical component of any industrial system. They allow you to control the flow and pressure of your fluid. Different valves can meet your needs depending on your application and how much pressure you need to handle. That said, there are several aspects to consider when choosing the right industrial valve for your application.
Besides the pressure and temperature requirements, you also want to check the material compatibility, connection types, and industry approvals. Some valves are rated for use in oil and gas, while others are ideal for food processing or drinking water applications. If you are new to the valve selection process, seek guidance from a trusted professional.