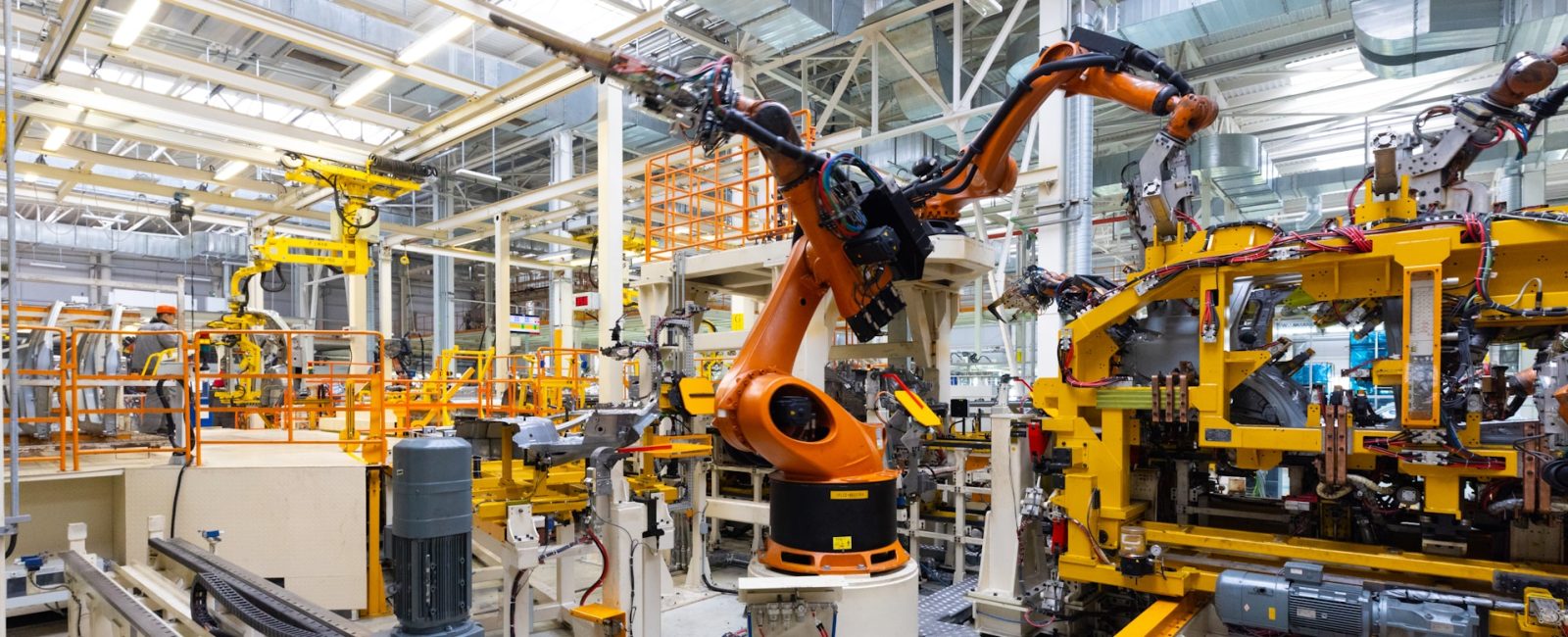
Relocating a factory internationally is no small task. Whether a business is expanding, seeking cost advantages, or adapting to new market demands, moving production facilities across borders involves intricate planning and execution. This complex undertaking goes beyond the logistics of packing and moving machinery. It encompasses legal, economic, cultural, and operational challenges that must be meticulously managed.
- Legal and Regulatory Hurdles
One of the most immediate challenges faced when relocating a factory internationally is navigating the diverse legal and regulatory environments. Each country has its own set of laws governing trade, labour, environmental standards, and business operations. Complying with these regulations is essential, as failure to do so could result in fines, delays, or even the shutdown of operations.
For instance, labour laws differ greatly across nations, affecting working hours, wages, and employee rights. Additionally, environmental regulations such as emissions standards and waste disposal requirements can vary significantly. Companies must ensure that their new location adheres to these local laws while also meeting international standards.
Securing permits and licences is another hurdle. Import and export laws, especially concerning specialised equipment, can complicate the relocation process. Customs duties, tariffs, and value-added tax (VAT) considerations further add to the legal complexities that businesses need to navigate.
- Economic and Financial Considerations
Relocating a factory internationally can be a significant financial burden, particularly in the short term. Companies must evaluate the costs of moving equipment, retraining or hiring new staff, and setting up operations in a new location. Furthermore, the economic environment of the destination country must be considered, including tax rates, inflation, and currency exchange fluctuations.
There may be economic incentives that encourage relocation, such as tax breaks, subsidies, or lower labour costs in the destination country. However, companies must weigh these potential benefits against the costs of relocation, which can include lost production time during the move, potential penalties for breaking leases or contracts in the current location, and the cost of adapting infrastructure to new regulations and standards.
- Supply Chain Disruption
One of the most pressing concerns when relocating a factory internationally is the potential disruption to the supply chain. Modern supply chains are often global, involving multiple suppliers from different countries. A change in the location of the factory can significantly impact how raw materials are sourced and how products are distributed.
Companies must carefully plan how to mitigate these disruptions. This could involve renegotiating contracts with suppliers or finding new suppliers closer to the new factory location. Additionally, the logistics of transporting raw materials to the new site and shipping finished products to customers need to be reconsidered, especially in light of potential border delays, tariffs, and transportation costs.
- Cultural and Language Barriers
Moving a factory to another country often means dealing with cultural and language differences. These barriers can complicate communication, both internally within the company and externally with local authorities, suppliers, and customers. For example, negotiation styles, business etiquette, and workplace culture may differ significantly between countries.
Additionally, language differences can create challenges in training new staff or communicating safety protocols and operational procedures. It is crucial to invest in translation services or bilingual employees to ensure that miscommunications do not lead to errors or safety hazards.
- Workforce Adaptation and Training
Relocating a factory internationally often involves either retraining the existing workforce or hiring new employees in the destination country. In either case, the workforce will need to adapt to new processes, technologies, and, in some cases, different regulatory requirements.
Training new staff can be particularly challenging if the new location has a labour force that is unfamiliar with the company’s equipment or production processes. The time and cost required to bring the new workforce up to speed can lead to delays in resuming full operations.
Furthermore, companies need to consider the potential loss of institutional knowledge when key employees from the original location are unable or unwilling to relocate. These employees may possess valuable expertise that is difficult to replace, further complicating the relocation process.
- Technological Infrastructure and Compatibility
Factories rely heavily on technology, from machinery and automation systems to software platforms that manage production and supply chains. When moving to a new country, businesses must ensure that the technological infrastructure is compatible with local standards. This includes power requirements, communication networks, and the availability of technical support.
For example, electrical systems vary across countries, meaning that machinery may need to be adapted or replaced to function correctly in the new location. Additionally, factory automation systems may need to be reconfigured to meet local technical standards or integrate with the new location’s supply chain infrastructure.
- Environmental and Community Impact
An international factory relocation can have a significant impact on both the local environment and the surrounding community. Companies must assess the environmental footprint of the new facility, ensuring that it complies with local environmental regulations and sustainability goals. Relocation may involve building new infrastructure, which can disrupt ecosystems or local communities.
Engaging with the local community is also important, as factory relocations can lead to job creation but also potential displacement. Managing this impact through corporate social responsibility initiatives can help maintain a positive relationship with the local population and minimise any negative consequences.
The decision to relocate a factory internationally is not one to be taken lightly. The process involves navigating a complex web of legal, economic, cultural, and operational challenges. From regulatory compliance to workforce adaptation, supply chain disruption to environmental considerations, each aspect of the move requires careful planning and execution. While the rewards of successful relocation can be substantial, such as cost savings, increased market access, and operational efficiencies.