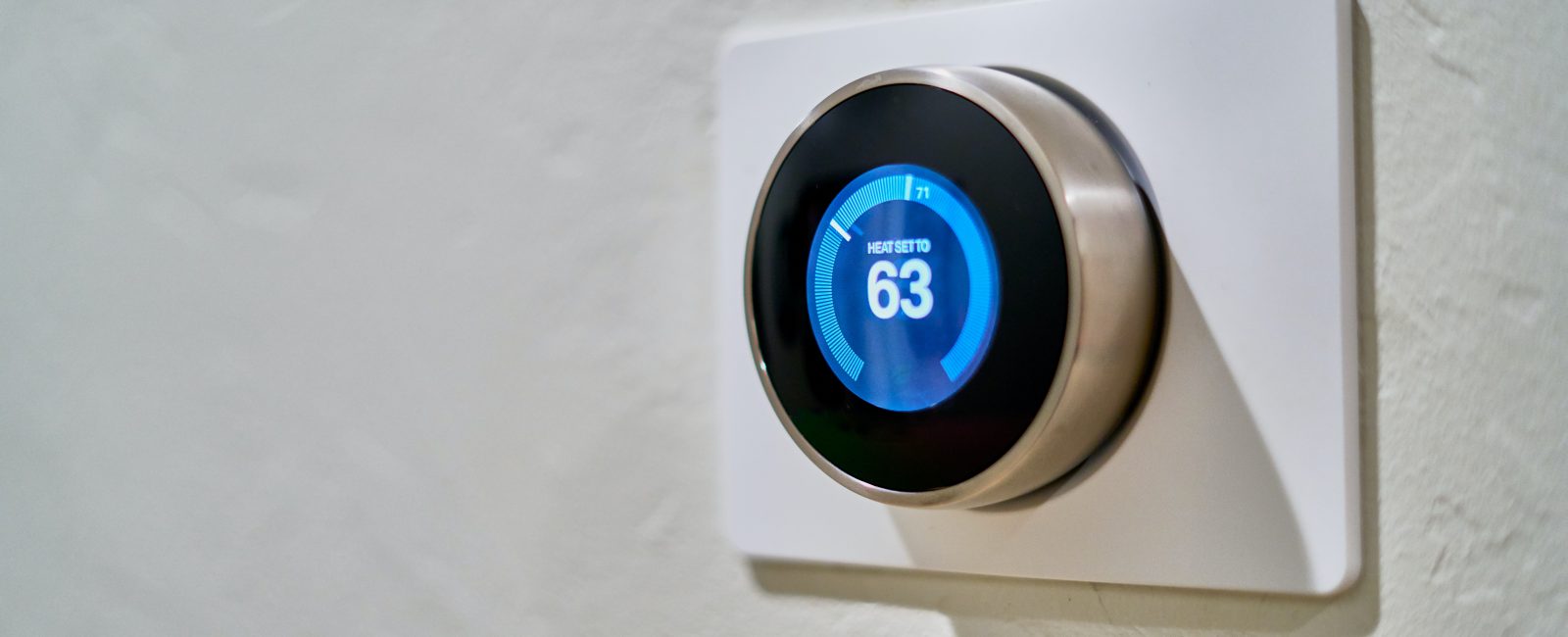
When it comes to definitions, there aren’t many more self-explanatory ones in the world of electronic devices as the temperature controller – as it literally does what it says on the tin. In a nutshell, it’s the catch-all name for instruments that control temperature, as it reads an input value from a temperature sensor, and then calculates by how much an associated heating or cooling control element needs to operate to get to the desired temperature.
Temperature controller types
There are a few basic types of temperature controllers. The ‘on-off’-type controller is the simplest, as it all it does is either turn on the control element, or turns it off. For instance, if it’s connected to a heater or a fan and the ‘set point’ is 50 degrees, the on-off controller will either turn on or turn off the control elements depending on the set point and the current actual temperature.
The second basic type of temperature controller is proportional control, whose key more advanced feature in comparison to the on-off type is to eliminate the constant on-off-on-off cycling around the set point. To do this, the proportional control instrument senses that the set point is being approached and will begin to either gradually slow down or speed up the average power delivered to the control element. In that way, proportional control devices are better able to keep temperatures stable rather than constantly above or constantly below the trigger set point.
PID temperature controllers
The explanations above lead us to the third and most sophisticated type of temperature controller – the PID temperature controller. The “P” stands for proportional controller, because the PID combines proportional temperature control with two other adjustment types that contribute to how well it automates the necessary system changes. The “I” stands for integral, representing a complex mathematical calculation adding up every temperature value that has been recorded, while “D” is a prediction of the temperature variance that will come next.
While it may sound complex, altogether it is the best, most accurate and most stable way to control temperature. Applications in which the set point, the amount of energy, or the mass that is being controlled change frequently are best served by the PID temperature controller.
For instance:
* Heat treatment in metals requires extreme temperature control to achieve the desired metallurgical properties.
* Even minor over-temperature conditions when drying or evaporating solvents on painted surfaces can damage the substrates, while minor under-temperature conditions can affect the finished product’s look.
* Top chefs or baking operations demand commercial and industrial ovens that heat up and then cool down in highly specific sequences, which is best done with sophisticated PID controllers.
The future of PID temperature control
The “P”, “I” and “D” principles date all the way back to mechanical devices from the 18th century, which helped steam engines from maintaining the ideal operating speeds. Nowadays, multi-loop PID controllers can manage a single process within multiple temperature zones – like the aforementioned complex commercial oven with many different heating elements in a single, simultaneously-operating application. And the future? As with every exciting technological advancement of our impressive times, the sky is always the limit.