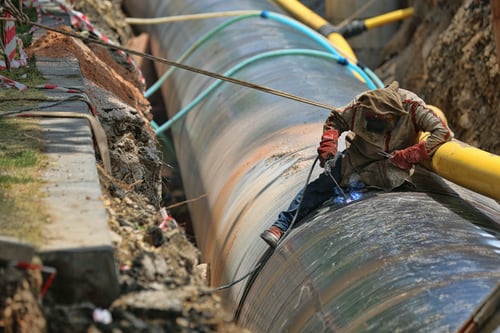
Our day usually starts with a hot cup of tea or coffee prepared on a gas stove or electric induction heater. We take this for granted and hardly ever think of how the gas or electricity is conveyed to our kitchens. Underground pipelines are the answer to transporting high pressure gas pipes and electrical cables. In addition, they are also responsible for transferring communication cables, water, various other necessities and waste as well. Besides these materials, underground pipelines are now used to transport solids, such as minerals or grains, over long distances as well as concrete, solid wastes, pulp, machine parts etc. over short distances. These underground pipelines are necessary for our lives to carry on without interruption, and they require protection at all times to prevent dangerous situations from arising.
We list below some methods to achieve this protection, one of which is the HDPE protection plates for buried networks. Besides the pipelines themselves being protected from internal and surface damage such as corrosion, they need to be protected from impairment from external sources as well.
Corrosion:
External coatings and internal linings to the pipelines themselves are necessary to prevent corrosion. External pipe coatings are used for cathodic protection of the exterior of the pipelines. Cathodic protection (CP) is an electrochemical method to prevent corrosion. The pipeline is made with the cathode (a charged electrode by which electrons enter a device) and another metal used as the anode, which gets corroded by the process instead of the pipe material itself. These external coatings form a barrier between the pipeline and environmental factors which could cause damage. To prevent internal corrosion, inhibitors are used by adding compounds to the pipeline which create a thin layer on the inside that prevents corrosion. The source of these inhibitors, of course, depends on the type of material that is being conducted in the pipelines.
Technology:
Modern technology, with the use of computers, is now used to control the transfer of materials through pipelines. Detailed information can be obtained to detect and prevent pipeline leaks or damage. “Smart pigs” (inspection devices that record information) are sent into the pipelines to detect and measure metal loss and internal corrosion. They can also detect curves in the pipelines. X-rays can detect flaws in welding. Communication between the headquarters and field workers is fast and action can be taken immediately to protect the pipelines.
Warning Meshes and Utility Protection Plates:
Another important factor which needs to be taken into consideration is the damage to pipelines from external sources, such as penetration by excavators during construction. To prevent such damage, Protection Plates and Warning Meshes are placed above the pipelines. They are usually light weight, made of HDPE (high density polyethylene), easy to install and can withstand collisions from excavators and other heavy materials. They offer a warning that pipelines are in place just below them and this lessens the risk of accidents and enhances safety measures. They can be custom made to the client’s requirements and carry relevant warning messages which are embossed on them. They can be easily removed for inspection checks or repairs to the pipelines and then replaced.
Conformity with designs and safety regulations:
All pipelines, protection plates and warning meshes need to conform to the rigid regulations before installation. If they are under designed, safety risks are enormous and hazardous situations could arise. Hence, they need to be statutorily approved with written authorisation. Risk assessments should also be made, taking into account the local environment.
Cleaning and regular checks:
Cleaning the pipelines on a regular basis will protect them. Pigging, a cleaning technique where trapped objects are recovered in the pipelines without hindering the operation, is used. Also checks, such as density checks of the embedment material and surrounding areas need to be done to ensure that the pipelines are protected.
Conclusion:
We realise that our underground pipelines need the utmost protection, not only to maintain routine in our lifestyles but also to avoid dangerous situations caused by damage to them. Following the above methods of protection, with the guidance of experts, will help in ensuring that our underground pipelines remain safe and protected.